Green Data Centers: Heat Reuse Options Every Facility Engineer Should Know
Introduction
Data centers are becoming pioneers in waste heat reuse, transforming the excess heat generated from their operations into valuable energy sources for local communities. These initiatives not only enhance energy efficiency but also promote sustainable living, showcasing the significant impact of innovative heat reuse practices worldwide.
From harnessing the heat from purified wastewater and redirecting waste heat into nearby buildings and district heating systems, to warming swimming pools, growing your own tomatoes and lobster breeding - there's no shortage of news regarding the continued stream of innovation.
It is important to note that waste heat is an undesirable byproduct of data centre operations. It represents waste that is paid for due to hardware inefficiencies. Therefore, reducing the amount of energy wasted can and should be the primary aim of operators and facility managers (how to do this is covered in an earlier article.) Also, the general industry consensus is that residual heat reuse should only be investigated following thorough energy optimisation initiatives.
Prior to data centers scaling up heat export, some major obstacles need to be overcome. Taking the UK as an example, the climate presents logistical challenges for efficient heat distribution due to seasonal changes and changing energy demand, which calls for careful planning and design. The viability of heat transfer is also greatly influenced by the availability and proximity of heat networks, with data centers situated in urban areas having an advantage over bigger remote ones in industrial areas.
Credit: White Paper on "Utilization of Waste Heat in the Data Center" A white paper by NeRZ in collaboration with eco – Association of the Internet Industry
The Law of the Land
The EU’s Energy Efficiency Directive (2023/1791) mandates energy performance reporting on the part of data centre operators, in addition to several references promoting the reuse of waste heat. I.e. Article 26.6 states 'Member States shall ensure that data centres with a total rated energy input exceeding 1 MW utilise the waste heat or other waste heat recovery applications unless they can show that it is not technically or economically feasible...'.
In 2023, Germany also passed their own ‘Energy Efficiency Act’ (EnEfG) mandating that DC’s avoid and reuse waste heat as much as possible plus make provisions with (municipal) heat suppliers. They also set specific targets for new facilities that go into operation on or after July 1st 2026 – with an Energy Reuse Factor target of 10%, increasing to 20% for those commissioned after July 2028. Special targets for PUE and renewable energy sourcing are also included - these requirements must be achieved at the latest pending a two-year optimisation phase after commissioning. Compliance with the specific ERF values could also be waivered if the operator formalises an agreement with the heating network operator to incorporate waste heat into their network, also, the wording in previous drafts ‘reasonable measures’ is not included suggesting ‘uneconomical measures’ would also have to be considered.
This drives DC developers to strongly consider the proximity and availability of heating networks during the site selection phase in addition to other parameters, as suggested in the 2024 Best Practice Guidelines for the EU CoC (Section 8.2 - Building Geographic Location).
In the UK, operators also need to be mindful of tightening legislation stemming from the ‘The Minimum Energy Efficiency Standards (MEES)’, the reduced CO2 emission targets in England’s ‘Building Regulations’ in addition to Heat Networking Policies via ‘Energy Act 2023’ – Chapter 2 (Prev. titled the ‘Energy Security Bill’). Heat network zones identified by local authorities will be incorporated into local plans, with new buildings and existing large buildings expected to connect to a heat network – modifications to existing systems may be required to ensure compatibility with the heat network. Consultations are ongoing regarding the details supporting the aforementioned. In parallel, Norway is following a similar zoning approach by stating its intention to compile a ‘national heat map’ to promote better utilisation of waste heat.
An interesting heat zoning proposal in London suggests if an existing District Heating Network is unavailable – major residential developments must incorporate a ‘communal’ heat network rather than traditional individual gas boilers for each premises. Thus, the UK’s approach tackles traditional investment challenges faced by heat network operators relating to high CapEx, long payback periods and connection agreement uncertainty by way of mandatory regulation within a prescribed timeframe.
Other non-regulatory incentives promoting heat reuse include potential tax relief schemes tied to energy reuse (Finland), planning criteria for new buildings to be ‘almost’ energy neutral (Netherlands) and governmental grants promoting heat recycling projects (New York, USA).
ERF, HRF, ERE Metrics vs PUE
Standards relating to the ‘Energy Reuse Factor (ERF)’ include EN 50600-4-6 and ISO/IEC 30134-6:2021, which articulate its definition, method of calculation and practical application – providing DC operators with the ability to measure how much of the heat they produce can be recovered and exploited. Likewise, the metric helps to quantify the efficiency of energy reuse practices – where a higher ERF indicates a more significant proportion of waste heat being repurposed. I.e. A value at 0.0 means NO energy is reused, while a value of 1.0 means all of the energy brought into the data center control volume is reused.
Thus, typical monitoring includes thermal energy transfers and temperature/flow rate conversion into equivalent energy units (KWh). Note, it may be worth quantifying building heat losses including those through the thermal envelope and other sources to validate if they have a negligible impact on ERF.
Note, whilst the ERF is a broad metric that encompasses all forms of energy reuse, the ‘Heat Reuse Factor (HRF)’ focusses specifically on heat energy. Which can be translated as the amount of thermal energy (in kWh) that is reused compared to the total thermal energy produced by the data centre.
Another metric presented by ‘The Green Grid’ includes the ‘Energy Reuse Effectiveness’ (ERE) which aims to counter misuse of PUE metrics (I.e. PUE’s <1.0) when calculating waste energy reuse scenarios. A lower ERE value would indicate better energy reuse.
In summary, the ERF metric is the most common out of the three – whilst a focus should also be maintained on how the energy is re-used after it leaves the measured data centre ‘control volume’ and that the overhead to reuse the energy doesn’t exceed the equivalent direct use of an energy source. For the most part, there is conflicting governmental legislation advocating residual heat reuse whilst at the same time driving lower PUE values. I.e. reusing residual heat often requires additional infrastructure and energy consumption, which can negatively affect PUE metrics. Finally, the PUE metric offers no credit or percentage points for generating energy or recovering waste heat – as this would divert from its primary focus.
Some notable case studies include a Swedish DC (2023) reporting ERF values of up to 0.66 (meaning 66% of the waste heat generated was successfully reused). Whilst Google’s Finnish ‘Hamina’ site boasts projections (2024) supporting 80% of the local neighbourhood’s heat demand proving there is indeed a heavy focus on achieving high ERF values.
Credit: energystar.gov
Heat Sources and Sinks
Some guiding principles can help developers ‘stay on track’ and reach their aspirations when developing waste reuse capabilities.
1. The waste heat should be reused locally.
2. Prioritise and cascade heat reuse, i.e. heating supply > district heating networks > cooling & power generation.
3. The incorporation of heat pumps to increase the available temperature plus the use of thermal energy storage to balance supply and demand should be assessed from both an economic and sustainability standpoint taking into account PUE targets.
It should be noted that for older legacy buildings, energy efficiency projects coupled with refurbishment may be cause for the reduction of the system temperatures as the facility becomes more efficient. While for new-builds, due consideration should be given to planned occupancy levels, server capacity and anticipated excess heat production during the initial launch stages – and the time required to reach full operational capacity – these are important factors for coordinated integration into potential reuse applications. The same goes for newer hardware – their replacement periods should be factored in (i.e. 3-5 year turnover), with heat projections accounted for taking into account improved efficiencies over time.
Below are some examples of typical waste heat sources in data centres and their respective potential applications.

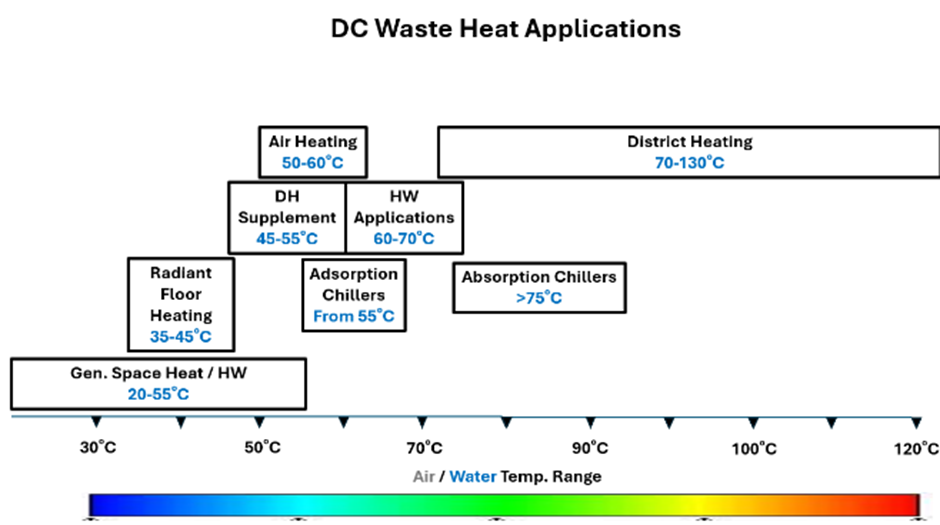
In summary, traditional air-cooled DCs provide more restricted opportunities for heat reuse due to their lower thermal quality albeit they form the lion’s share of the market. Therefore, the use of heat pump technologies is key (especially so for heat transportation over distance) to upgrade the heat including integration with next generation district heating systems that take can advantage of increasingly lower heat inputs.
Heat pumps however also put more pressure on the grid (with a potential negative impact on PUE targets as discussed in the previous section) and thus their consumption, local energy prices and the availability of renewable energy sources needs to be considered. For example, high energy prices in Germany currently present a major challenge for the financial viability of heat pumps and related infrastructure used for waste heat recovery.
Likewise, liquid cooled servers provide greater opportunities for direct reuse, however their wide-spread application is limited.
An important consideration is that heat reuse applications also have limitations on how much heat they can physically absorb and are subject to ambient conditions which may alter the volumetric flow of waste heat. Thus, design parameters must include a degree of ‘compensation’ to cater for different seasons and potential reduced volume flows. An example of this can be seen when comparing colder regions (i.e. Scandinavia) which have substantial heating demands and countries such as the UK where the weather fluctuates – the heat distribution needs to be adjusted seasonally to cater for lower demand during the summer. In conclusion, the key target is to ensure efficient use of DC generated heat throughout the year.
Finally, some typical KPIs to consider when assessing heat reuse initiatives include:
· Waste Heat Recovery % from IT equipment / WHR Potential (MWh/year)
· PUE % Improvement.
· Total Electricity Use / Op. Cost Saving (%)
· Payback period (years)
Who Wants My Heat?
As previously highlighted, long-term heat reuse investments should be considered based on a fully optimised data centre running in a steady-state condition (i.e. fully operational, stable IT load). Seasonal fluctuation plus variable energy demand are also factors that should be considered. Likewise, the proximity and availability of heat networks are critical plus agreement on who will pay for connection costs.
Heat mapping is the obvious first step to confirm the existence of a heat outlet at a reasonable distance or a pre-existing heat network that can receive extra capacity. In summary, there needs to be a successful match between the DC heat output and local heat consumers i.e. space and hot water heating in schools, hospitals, laundrettes, local residential areas, commercial properties, offices, gyms, restaurants, hotels, leisure centres plus industrial facilities that need thermal input.
Another interesting heat recipient is wood pellet manufacturers as showcased by EcoDataCenter’s Swedish facility, where waste heat contributes to biomass drying processes to achieve optimum moisture content.
In terms of agricultural reuse, greenhouses – particularly vertical farming and aquaponics (combined fish and plant cultivation) facilities can benefit greatly from heat reuse initiatives due to their cultivation of fruit, vegetables and algae all year round plus offer high yields. The temperature range required for this application is well suited to what DCs typically provide. Other agricultural products can also be produced including flowers and aromatic plants.
Potable water production can also be achieved via vacuum distillation, using waste heat transferred as hot water. Seawater can thus be boiled at a lower temperature (under vacuum) and effectively desalinated – producing both water for drinking (the norm in the marine industry), irrigation and other uses. Other vacuum distillation applications include effluent treatment of machining coolant – I.e. supplementary waste heat can significantly lower the energy costs of such facilities.
Anaerobic digestion as used in domestic and industrial wastewater treatment also requires heat between 35ºC-57ºC depending on the setup to accelerate microbial activity and thus breakdown of organic matter. Temperature control is also a key parameter for nutrient rich ‘biosolid’ sludge treatment, a byproduct of wastewater treatment – waste heat can be used to effectively dry the sludge making it more cost-effective to handle and reuse for soil conditioning or as feedstock for other heat source applications.
Thus, in the initial concept phases of data centre design, forward-planning is crucial to identify adequate opportunities which may also include potential colocation with the above-mentioned applications, in addition to keeping abreast of future expansion plans for local and district heating networks. New industrial ‘data parks’ are also coming online that provide a secure and redundant power supply with a guaranteed fibre network – in addition to a waste heat reuse connection.
Credit: White Paper: Utilization of Waste Heat in the Data Center - Eco
5th Generation DHNs
Fifth generation district heating and cooling (5GDHC) systems (also known as ‘ambient loop’ networks) operate closer to ground (ambient) temperature by incorporating lower temperature renewable heat sources (<25ºC) and by utilising seasonal & medium temperature thermal storage (e.g. aquifer thermal energy storage or former coal mines – Heerlen, Netherlands) to balance demand. They are also bi-directional - recuperating generated heat from cooling and vice versa, generated cold from heating.
They are also ‘decentralised’ in nature, thus not constrained as per previous generation networks where heat is supplied at the temperature required by the most demanding end user. The fundamental goal of such systems is to move consistent temperature heat between multiple sources and likewise, users – in a shared distribution system with lower CapEx and OpEx expected due to its decentralised nature as opposed to housing a larger single centralised heat exchanger. Thus, another key aspect is that each building connected to the network has its own heat pump, extracting heat from the loop in the winter to provide heating and rejecting heat into the loop in the summer to provide cooling.
There are several opportunities to accelerate both the creation of such networks plus enhance their cost-effectiveness, which include the development of renewable energy sources for heat pump power demands, ‘plug and play’ connections for renewable heat sources and consumers respectively, in addition to the creation of prefabricated ‘energy’ substations.
Finally, 5GDHC systems have the ability to integrate renewable energy sources such as geothermal, solar thermal, etc. in addition to waste heat processes. Even ‘wastewater’ in city drainage systems and WWTPs can act as contributors via a combination of heat recovery units, heat exchangers and heat pumps (housed in an energy centre) - utilising average sewage temperatures ranging between 15-30ºC (Ref. Scottish Water Horizons’, Kalundborg’s and Vancouver’s case studies respectively).

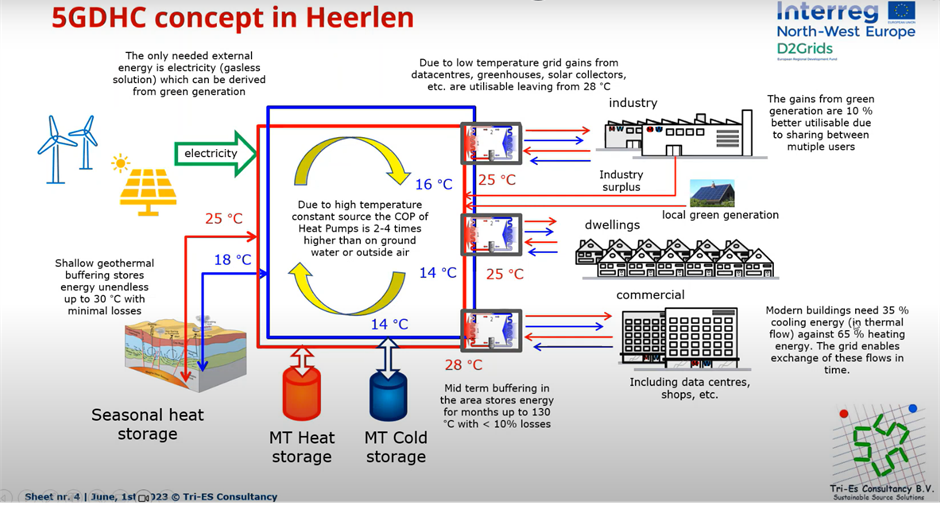
Heat Pumps
The basic principle of heat pumps is that they extract heat from a lower-temperature (LT) source such as water, ground, air or waste heat (i.e. rivers, sewage, ground, geothermal, flue gas, waste heat, etc.) and amplify it to a useful temperature, transferring it to where it’s needed. The pump system is modelled on a closed-loop refrigerant cycle enabling both compression and expansion of the refrigerant. Some configurations include a reversing valve that allows the system to act bi-directionally to deliver both heating or cooling, this works by redirecting the refrigerant, causing the condenser to function as the evaporator and vice versa.
Likewise, electricity is needed to power the compressor, whilst the heat pump efficiency is represented by the rated coefficient of performance (COP). Carbon neutral heating and cooling can be achieved if powered by renewable electricity.
Credit: Berg-Group
When scouting for different heat pumps, you will come across various terms including standard, supercritical, multi-stage, high-temperature (HT) and very-high temperature (VHT) - in essence they are all designed to serve different operating temperature ranges and applications. Typically, when you start looking at highly fluctuating head loads and higher temperature applications - the advanced material requirement, system complexity and cost...go up.
Different heat pumps use different types of compressors based on their specific requirements, such as capacity, efficiency, cost, and application. Reciprocating compressors are commonly used in smaller systems, such as residential and light commercial applications. Screw type compressors are suitable for medium to large heat loads, such as those in commercial and industrial settings. Whilst for large-scale applications with high heat loads, centrifugal compressors are used for district heating and industrial processes.
Other types of compressors may be specified i.e. scroll compressors for their reliability, efficiency, low-noise and low vibration or rotary compressors where compact footprint and low cost is a priority. Some compressors are better suited according to the refrigerant they use. Whilst some perform better under varying temperature and pressure conditions, i.e. for specific climates and applications. Thus, it’s important to fully assess the budget availability, operational requirements, environmental objectives and climatic conditions when reviewing prospective heat pump models.
Industrial heat pumps do use refrigerants which are essential for the heat transfer process, i.e. absorbing heat from a source and releasing it at a higher temperature for reuse in other applications. Some of the leading industrial heat pump manufacturers including GEA, Oilon, Araner, Danfoss and MAN ES offer a selection of models that use R717 (NH3, Ammonia – efficient but toxic), R290 (Propane – efficient but highly flammable), R744 (CO2), R1234ze (HFO – a synthetic replacement for R134a) in addition to HFC based refrigerants such as R134a.
In summary, suppliers are transitioning to lower GWP refrigerants, driven by market pressure and regulations such as Europe’s revised F-gas regulation (EU 2024/573) that came into effect in March 2024 in addition to future market bans on refrigerants that exceed specified GWP thresholds that vary by product type.
Operational considerations when assessing refrigerant suitability include COP, retro-fit capability into existing systems, effectiveness in cold climates, flammability and proximity to sensitive receptors (i.e. apartments and terraced houses) plus the need for specialised equipment (as with CO2 due to higher pressure and lift temperature required).
When attempting to design, match and optimise the sources and sinks in prospective heat pump systems, several key steps are required:
1. Evaluating Heat Sources
Temperature Stability: Choosing sources with stable temperatures throughout the year, such as groundwater or deep wells.
Availability and Proximity: Selecting sources that are readily available and close to the heat pump to minimise energy losses.
Environmental Impact: Considering the environmental effects of using the chosen heat source.
2. Assessing Heat Sinks
Demand Matching: Ensuring the heat delivered meets the demand of the heating or cooling application.
Temperature Requirements: Matching the temperature output of the heat pump to the requiredtemperature of the application.
Distribution Efficiency: Using efficient distribution systems to reduce energy losses.
3. System Design and Integration
Heat Exchanger Efficiency: Optimising the design of heat exchangers to maximise heat transfer between the source and the sink.
Controls and Automation: Implementing advanced control systems to regulate the operation of the heat pump based on real-time data. Important!
Maintenance and Monitoring: Regular maintenance and monitoring to ensure the system operates at peak efficiency.
By carefully selecting and managing these elements, heat pump systems can operate more efficiently, reduce energy consumption, and provide cost-effective heating and cooling solutions.
Some other features to assess when selecting heat pump systems include:
þ Fast start up and stop capability,
þ Remote operation with 24/7 monitoring,
þ High availability, redundancy, maintenance requirements, etc.,
þ Seasonal coefficient of performance,
þ Auxiliary equipment and footprint requirements,
þ and the big one...Total cost of ownership (unit cost, installation, energy, maintenance, etc.).
Credit: Carrier Ultra-Low GWP HFO Heat Pumps Help Decarbonise the City of London
Finally, the RED III (Renewable Energy Directive III) aka Directive (EU) 2023/2413 entered into force in November 2023 replacing existing EU directives relating to renewable energy. It strongly supports the adoption of high efficiency heat pumps and sustainable heating/cooling applications, plus simplifies the permitting process for heat pump installations, facilitating wider adoption, which is a massive boost for the sector.
Credit: MAN-ES
Cooling via Waste Heat – Chemical and Thermal Compression
Heat can also be utilised to produce cold, thus reducing the need for electrical cooling. For this use, adsorption and absorption chillers are used. There are numerous benefits to using these sorption chillers. Specifically, this makes it possible to perform refrigeration without using F-gases, which are detrimental to the environment. Adsorption chillers are suited for small outputs of 10 kW and more, and they can already run from as low as around 55°C. While absorption chillers are often operated in power classes greater than 200 kW and require a heat level of 75°C and more for operation.
When combined with data center waste heat, there are several benefits. In this approach, various components inside or outside the data center can be immediately cooled by the heat produced in the facility, especially during the summer. This makes it possible to use waste heat all year round. This kind of approach works very well if the IT systems are water-cooled and there is water available that is at least 60°C in temperature.
Absorption chillers work via chemical compression, while efficient and able to handle different heat sources for a variety of applications - they do come with certain EHS considerations which include chemical and environmental hazards in the case of leakage or exposure stemming from their use of water/lithium bromide salt (corrosive, non-toxic) or ammonia/water (toxic) solutions – where the former is more common whilst the latter can serve lower temperature cooling requirements.
In the case of water/bromide solutions, water serves as the refrigerant and lithium bromide as the absorbent. Care should be taken regarding improper mixture concentrations or operating temperatures outside the design range that can lead to crystallisation and subsequent system blockage. Also, whilst they effectively give ‘new life’ to waste heat, the external electricity supply requirements and expected energy consumption should be carefully assessed. That said, the expectation is that they consume significantly less than traditional vapor-compression chillers.
Some key parameters to watch out for when comparing equipment includes the COP which for absorption chillers can be significantly lower than mechanical chillers, this is because thermal energy is less efficient in driving the cooling cycle compared to mechanical compression used in electric chillers. Also, the chiller should be sized correctly – if oversized for a particular application, lower operational efficiencies can be expected. These systems also perform well in DCs when the waste heat temperatures ranges between 65-100◦C. However, operational issues are reported both under low-temperature conditions <65◦C and also high ambient temperatures where the chiller may struggle to reject heat effectively, this is coupled with their low power to weight ratio – i.e. their footprint may not be suitable for sites limited on space. Finally, due to the corrosive nature of the absorbent material, the maintenance requirements (understood to be high) and use of hazardous corrosion inhibitors (which impact EoL decommissioning) need to be fully understood – in addition to how by-products of the cooling process are managed which reportedly include hydrogen offgas, typically managed by a palladium cell inside the chiller unit. Start-up times are also reported to take up to 30 minutes with the need for a strict shut-down protocol.
For adsorption chillers, which work via thermal compression, solid adsorbent material is typically used (desiccants such as silica gel, zeolites and activated carbon) to adsorb a refrigerant (typically water) – this combination is considered non-corrosive and environmentally friendly with reduced maintenance costs compared to the absorption variants already mentioned. The CHW output temperature is also lower (5-10◦C) compared to absorption variants (>9◦C).
This cooling technology also suffers from a low COP compared to mechanical chillers, and slightly lower than their absorption chiller counterparts. Also, they require multiple bed design configurations to maintain continuous operation as the adsorption – desorption cycles require periods of both heating and cooling.
In summary, whilst absorption and adsorption chillers both offer a promising avenue for waste heat – the technicalities of their operation combined with CAPEX, OPEX, footprint, etc. need to be carefully considered. It is also important to consider the operational cooling requirements as both set-ups are reported to have slower response times (due to thermal inertia, heat-cool cycling, etc.) than conventional chillers, which is a major disadvantage for applications that require rapid cooling adjustments, i.e. highly fluctuating loads.
Credit: Bryair
The Organic Rankine Cycle – Electrification of Heat
An Organic Rankine Cycle (ORC) is a thermodynamic process that converts thermal energy into mechanical power using an organic fluid with a lower boiling point than water, applicable for medium-high temperature heat sources ranging from 80 to 400°C and for small-medium applications at any temperature level. It differs from traditional steam turbine alternators in that no superheating is required therefore blade erosion is mitigated via dry expansion in the turbine. A Micro-ORC is a scaled-down version of the ORC designed for very low power applications where space and heat source availability are limited. This video (here) by Turboden provides an excellent overview of the capabilities of this technology.
Credit: Turboden
For decades, the traditional choice of expander for ORC cycles worldwide has been to employ axial or radial inflow turbines. Exergy introduced an innovation utilising a Radial Outflow Turbine (ROT). Benefits include Higher Efficiency, Simplified Design, Better Performance with Low-Grade Heat and Compact Size. Considerations with this design include more complex manufacturing requirements, scalability for very large power outputs, mechanical stress impacting lifetime and both reliability & efficiency at high flow rates.
As mentioned, the working fluids are organic in nature, i.e. refrigerants for low-temperature ORC - which are subject to the same F-gas regulatory trends as discussed in the heat pump section. For high-temperature applications, the fluid is a hydrocarbon, which is the best option to extract the maximum power from a warmer feed. Example fluids include benzene, methanol, toluene, and cyclohexane. Exposure limits and guidelines for use are regulated under OSHA and EU REACH regulations - one should be very mindful of occupational health and flammability impacts. Silicon fluids are also used in some products, with advantages including thermal stability, non-flammability, chemical inertness.
This below resource provides a fantastic overview of all Organic Rankine Cycle units installed globally.
Credit: KCORC.ORG
Looking at a few leading suppliers, Enertime’s OCR utilises waste gas and hot air at temperatures over 250ºC plus liquids and steam over 130ºC. It also uses R1233zdE and R245fa for their medium temperature product and HCs for higher temperatures. R1233zd is classed as an HFO rather than an HFC. HFOs are a newer class of refrigerants designed to have very low GWP and ODP parameters. Whilst R245fa is an HFC. This class was developed as a replacement for ozone-depleting CFCs and HCFCs, but they still have a relatively high GWP compared to newer alternatives like HFOs.
Orcan Energy’s PACK product line is suitable for waste heat ranging from 80-800ºC, with R245fa as the working fluid. Electratherm’s product range includes the ‘Power Module 75’ can be directly integrated with a cooling package, with hot water inputs ranging between 65-132ºC whilst the ‘Power+ Generator’ requires waste heat ranging from 70-150ºC (liquid) and over 150ºC (gaseous) – again using P245fa.
Turboden publishes case studies of various setups globally, with many installations in the cement, steel, glass, biomass power and metals sectors – all industries that generate significant amounts of waste heat during their processes. The below global market outlook highlights the main users of this technology.
Credit: Grandview Research
Vertiv have published a very relevant white paper titled ‘Experimental lessons of an organic Rankine cycle applied for waste heat recovery in a data center environment’. A demo ORC system replicating a 30kW liquid-cooled server rack was tested to capture the server waste heat and convert a portion to electricity while transporting the heat to ambient air. The unit utilised a low GWP non-toxic working fluid. The conclusions remark a 2% conversion of waste heat into energy, with approximately half of the energy available consumed by the unit pump in addition to extra energy required to release the remaining waste heat - thus ending up as an energy consumer. In a data centre, the heat reuse application would need to run all the time, handling temperature ranges throughout the year. The study also noted the ORC wasn't stable enough to cater for the hottest days at the trial site, thus discounting it as a sole means of cooling in a DC environment.
Credit: ORC-LITE SERIES
Thermoelectrics - The Stuff of Sci-fi
Thermoelectric cooling technology (known as solid-state due to the absence of refrigerant) converts heat directly into electricity that can in turn be converted to cooling. Although it’s a promising method for waste heat recovery, its commercialisation has been limited due to low conversion efficiency and high costs when applied to larger physical areas.
Likewise, for specific applications such as remote power generation (NASA use it to power deep-space devices where solar energy isn’t available) or small-scale waste heat recovery where there isn’t enough space to house mechanical cooling, it can be a viable option. Recent advancements however, especially in nanotechnology, have improved efficiency, renewing interest in this technology. For example, Phononic is a company that specialises in thermoelectric cooling solutions for data centers, they use Thermoelectric generator (TEG) devices to convert waste heat from servers into electricity, which can then be used to power cooling systems or other equipment. The effectiveness of this offering would have to be assessed on a case-by-case basis.
The technology also requires large temperature differences in order to reach efficiencies of just a few percent, giving rise to the development of thermomagnetic generators which use materials with temperature-dependent magnetic properties – useful in applications where traditional TEGs are less efficient due to the small temperature differences mentioned.
Heat Storage
There are various types of heat storage systems that are relevant to DC waste heat reuse, some commercialised and operational, with others still in development. A quick summary is tabulated below - where we already mentioned an example of Aquifer Thermal Energy Storage (ATES) in the 5th Generation DHN section.
Sensible Heat Storage: This is the most widely used and commercialised method. It involves storing heat in water or other materials and is commonly used in DCs for cooling and heating purposes. A good example of an SHS setup is showcased in Copenhagen's District Heating System. The heat is captured and stored in large water tanks, then distribute through a network of insulated pipes to provide heating for residential and commercial buildings in the city.
Molten Salt Storage: This method is used in concentrated solar power (CSP) plants and has been commercialised for large-scale thermal energy storage. Molten salt is used to store thermal energy collected from the sun during the day. The molten salt, heated to high temperatures, is stored in insulated tanks. When electricity is needed, especially during the night or on cloudy days, the stored hot molten salt is pumped to a heat exchanger to produce steam, which in turn drives a turbine alternator. After transferring its heat, the cooled molten salt is recirculated back to the storage tanks to be reheated, ready for the next cycle.
Latent Thermal Energy Storage (LHTES): Some commercial applications of LHTES exist, particularly in building heating and cooling systems, where heat can be captured using next-generation salt-based phase change materials (PCMs) that are embedded in building materials like walls or floors. During the day, the PCM absorbs excess heat, storing it as latent energy. At night, the stored heat is released from the PCM, helping to maintain a more consistent temperature thus reducing the strain on traditional HVAC systems.
Borehole Thermal Energy Storage (BTES): BTES systems have been implemented in some regions for seasonal heat storage, such as in the city of Vaasa, Finland. In this setup, waste heat is captured and stored in boreholes drilled into the ground. During the warmer months, excess heat is injected into the boreholes and stored underground. When heating is needed during the colder months, the stored heat is extracted and distributed to residential and commercial buildings via insulated pipework.
Heat for Sale
The benefits of waste heat reuse are generally demonstrated through a combination of energy savings, carbon emission reduction and economic analysis.
To put things in perspective, a decreased heat output will not be sufficient to recover the original investment (for a heat network connection) made by a data center if the center fails to achieve the necessary occupancy levels or sees a fall in occupancy over time. Also, industrial concerns have been expressed regarding unstated expenses related to joining a heat network (i.e. receiving a bill for cooling energy.) This reinforces the importance of solid contractual agreements between data centers and heat network providers. While both data centres and heat networks could financially gain from the sale of heat, the implementation of heat recovery introduces additional financial risks to a business.
Another example is Stockholm's Exergi’s district heating model - where they invest in the network connections, while data centres and other industries invest in the heat pumps. The payment model facilitates businesses selling their excess heat to Stockholm Exergi based on a projection of the costs that would have been incurred to produce that heat in a different way: approximately €190,000 per year per MW of heat delivered.
Likewise, various heat pump calculators are available online including that provided by GEA. It’s important to conduct thorough cost-benefit evaluations for any project relating to waste heat reuse.
Credit: GEA
Synergies with other techs – Green Hydrogen
Green hydrogen is produced using renewable energy sources. By using waste heat from data centers, the efficiency of electrolysers (devices that split water into hydrogen and oxygen) can be enhanced as less energy is needed to physically heat the water. This integration can lower the energy requirements for hydrogen production, making it more sustainable. Siemens Energy is entering this space with their integrated electrolyser and heat pump solution.
Credit: Siemens Energy - Integrated Electrolyzer and Heat Pump Solution
We hope you found this article useful!
If you are looking for professional feasibility study and cost-benefit analysis support, or turnkey project management relating to any aspect of your next industrial mega-facility design & build project...
Contact — Biyat Energy & Environment Ltd (biyatenergyenvironment.com)
This article was written by Luay Zayed, Founder' of Biyat Energy & Environment Ltd. A global energy and environmental consultancy specializing in turnkey engineering solutions that protect the environment and improve energy efficiency in the manufacturing & industrial sectors.